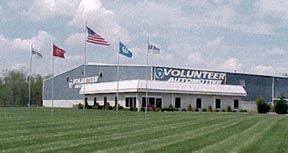
Volunteer Automotive's Airtime-Free private 2-way radio system provides increased productivity and greater safety for workers!
Manchester, Tennessee - Population 8294, is
believed to be the home of more automotive parts manufacturers than any other
city of comparable size in the USA. With several large auto manufacturers in
close proximity, the thriving community of Manchester, conveniently located in
mid-Tennessee on Interstate 24, is ideally suited for efficient
distribution. Volunteer Automotive, Inc., with a work force of over 200,
is one of these specialty parts manufacturers with a claim of producing over 30%
of all fuel filler doors for all vehicles produced in the USA! As a metal
stamping manufacturer, Volunteer makes those things that don't get all the
attention, but are very necessary for the efficient production of US
manufactured vehicles. In addition to fuel filler doors, Volunteer
Automotive manufacturers all types of metal products such as dashboard brackets,
seat brackets, etc. for auto makers including BMW, Ford, GM, Nissan, and others.
Volunteer Automotive has always been on the leading edge of improvements in
plant efficiency and safety. As an ISO/TS 16949 certified manufacturer,
the company takes pride in acknowledging an even higher level of quality
standards than the more commonly known ISO 9001 standard. More
importantly, the company complies with the safety and environmental requirements
of ISO 14001. Meeting current safety standards requires an effective means
of communications, especially for monitoring the activities of workers involved
in confined space activities. The horror story of a worker who had fallen
on a piece of metal in another plant (not associated with Volunteer Automotive)
is well known. The worker died as a result of his 2-way radio being in a dead
area. All attempts to call for help were in vain. The worker
bled to death as a result of ineffective communications. Good in-plant
communications is not just a convenience - it can save lives! Adherence to
quality and safety requirements are known benefits of effective wireless
communications. However, there are other benefits of a more tangible
nature.
Joe Wilburn, maintenance facilities manager at Volunteer Automotive summed up the
benefits of effective 2-way communications when asked the benefits to his
activities. His two part answer says it all - I couldn't operate
without them and they save me about a hundred miles of walking per day!
These answers may be slightly exaggerated, but they are pretty much the answers
given by other plant operations managers all over the USA.
Volunteer Automotive didn't start with 2-way way communications. The
company started with one-way paging. Supervisors and maintenance personnel
could be paged by the receptionist and they would then return the call from the
nearest telephone. This was working fairly well until company management
decided it wasn't needed. The maintenance department purchased a few 2-way
radios that worked well for their needs. The only problem was the cost of
the radios. The models used at that time were fairly expensive and costly
to maintain. As additional radios were added, lower cost models were found
and other supervisors began noticing the benefits of 2-way communications.
The decision was made to expand the use of the 2-way radios to allow supervisors
to communicate with each other. There was some concern that potential user
conflict might occur between administrative and maintenance users sharing a
common frequency. The Nextel system was reported to provide the capability
of individual calling which appeared to be a possible alternative. As it
turned out, the Nextel system required payment of monthly airtime charges in the
amount of $34 per unit used, and that rate was based on a minimum commitment of
30 units. In addition to the $1,020 monthly cost, an additional expense of
$5,000 was required to provide coverage inside the buildings. To make matters
worse, the Nextel system did not address the real needs of plant operation -
specifically group calling. The company learned that they would have to
pay additional surcharges to allow groups of people to communicate with each
other The better solution proved to be one of establishing two radio
channels for the 2-way radio system - one for administration, and one for
maintenance.
Things were going pretty well until a new warehouse facility was constructed a
half mile away from the main plant. Good quality 2-way radios are capable
of providing operating ranges of up to two miles, but not from inside one
building to the inside of another building. The coverage in the new
warehouse building proved to be unreliable. The local 2-way radio dealer
was contacted and asked to provide a solution. After waiting several weeks
for a response, the name of Falcon Wireless came up. Bobby Henley, a
volunteer with the local fire department mentioned to Todd Patterson, the plant
manager, that Falcon Wireless had always been responsive to their needs.
It was decided to contact Falcon for a possible solution. The task was
given to Gail Ashby, the Administrative Assistant to Joe Wilburn.
Falcon's recommendation involved a two part plan. The first was to provide
radios capable of utilizing more than two channels and with the ability to allow
priority scanning. This would be a preparatory step toward the addition of
a repeater station capable of covering both the original plant area and
the new warehouse. The radio selected was a professional grade Motorola
model with 4 channel priority scanning and memory free Nickel Metal-Hydride
batteries. The proper disposal of batteries was an on going concern since
EPA regulations require proper disposal. As a part of Falcon's services,
the company offered to dispose of all batteries shipped to them by Volunteer
Automotive at no cost. All that was required by Volunteer Automotive was
to pack them up and ship them to Falcon.
The new repeater channel is used for all calls originating from the receptionists
desk with all radios tuned to the repeater channel. With the new system,
the receptionist not only has the ability to call administrative and maintenance
personnel but to receive a direct acknowledgement without the called person
being required to find a phone. The older two channel radios operate in
the repeater talk-around mode that allows them to communicate with each
other without disturbing the receptionist and at the same time being able to
hear any calls initiated by the receptionist or other users on the system.
The system utilizes the original two channel Motorola P110 radios as well as the
Motorola SP50's and the newer Motorola CT250's. The SP50's and CT250's
have active third and fourth channels which can be used in private as desired.
One of the key issues required by Volunteer Automotive is prompt response to
their needs. As a company required to meet the demands of rapid response
customers, those same capabilities are required of their vendors. The key
interface person between plant operations and Falcon Wireless, Gail Ashby, notes
that Falcon has been extremely responsive and understanding of our needs.
Falcon has been careful to explain the various maintenance options available and
assisted us in defining the most cost effective service for our requirements.
Today, the radio system is being used by supervisors, tool and die personnel,
materials handlers, and the original maintenance users. All agree that the
ability to provide cross departmental communications is a valuable asset in
terms of saving time, improving efficiency, and increased safety. The
company currently uses remote activated light boards to allow machine operators
to signal maintenance and supervisory personnel of a malfunction.
Unfortunately, unless the desired party is looking at the sign, the urgency of
the situation is unknown. Since a production stoppage of a machine can
cause expensive delays and wasted labor cost, the ability to quickly notify the
proper person in the event of a breakdown is extremely important.
Falcon Wireless is currently in the planning stages of offering inexpensive
radio call boxes located strategically throughout the plant to minimize the
downtime associated with equipment malfunctions. Although not yet
installed at Volunteer Automotive, the advantages of this system over the
current light boards may warrant yet another investment in wireless
communications. As it has often been said - good communications doesn't
cost - it pays!
If you would like to know more about how you can make your plant a safer and more efficient workplace, please give us a call at 1-800-489-2611. We think you will be glad you did! |